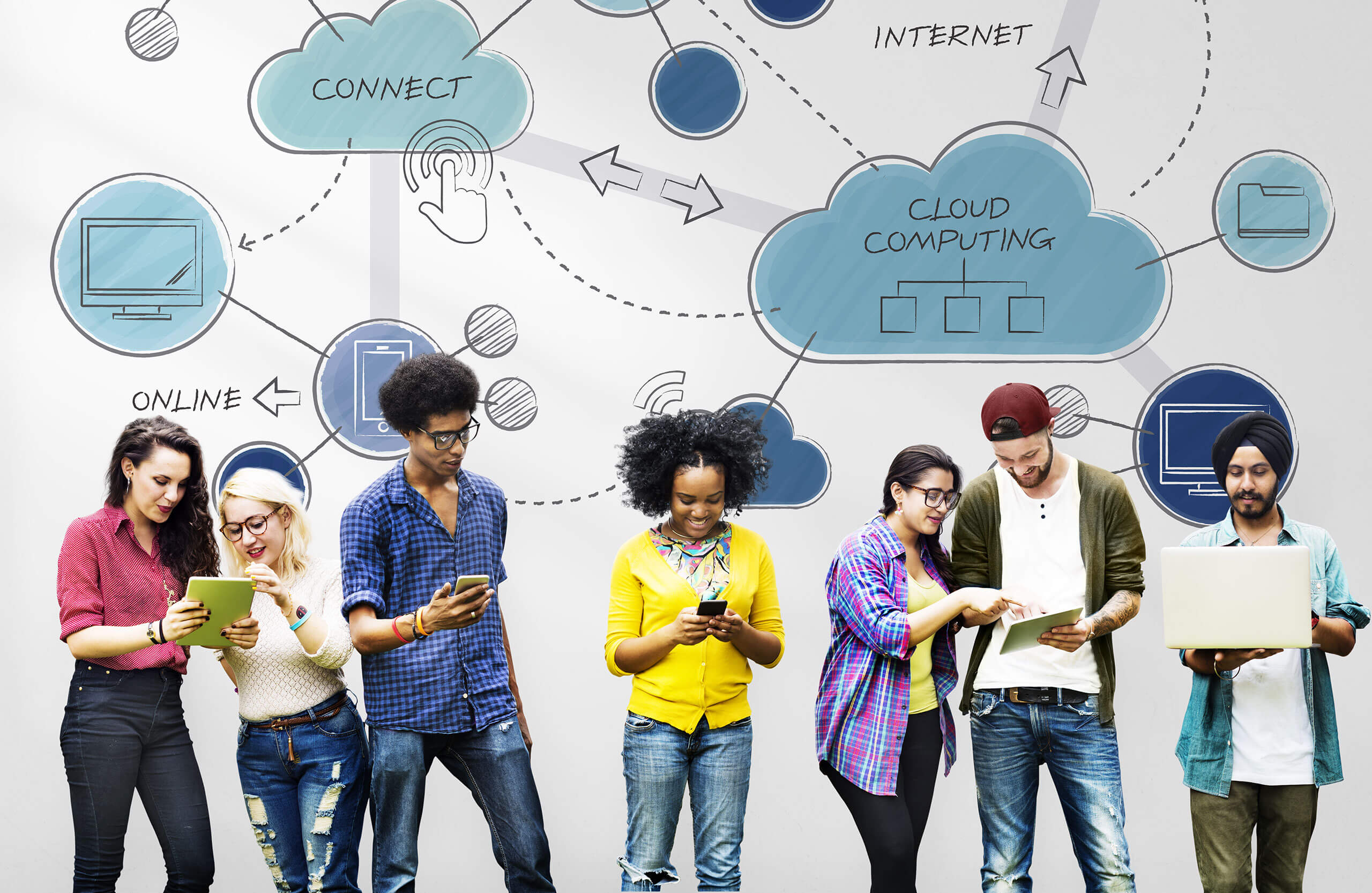
Electronics devices have become indispensable to everyone. Imagine life without your cell phone or your laptop. Perhaps for a few seconds you imagine a blissful peace and quiet, but pretty fast you realize exactly how much of your life is entwined with these devices – from your employment, your social life, your treasured memories, your hobbies and entertainment, to connecting with the most important people in your life. Electronic devices have quickly become tools we can’t function without, as the capabilities built into these ever smarter, faster and smaller devices continue to improve, this is unlikely to change.
One thing that is changing rapidly is the amount of heat generated by the devices as they become more and more capable. The increased processing power required to provide all the functionality we take for granted is generating more and more heat. To enable devices to perform as you expect, protecting their electronic components and your important data, devices need effective cooling.
Until recently, device manufacturers were limited to choosing either passive or fan based active cooling – both options have frustrating pros and cons that need to be considered.
Now, innovation in heat removal has finally caught up with innovation in device capabilities. Manufacturers, and consumers, now have a third, better option for heat removal – “Solid-State Active Cooling”.
Ultimately, effective cooling determines how much performance you get from your device. So now, just as consumers have been paying attention to the CPU spec or memory size, they are now looking for the thermal solution that gives them the highest performance and other benefits.
Below is a summary of the three approaches to cooling electronic devices and the pros and cons of each:
THREE APPROACHES TO COOLING ELECTRONIC DEVICES
Passive Cooling:
Principle: Passive cooling relies on natural heat dissipation mechanisms, such as conduction, convection, and radiation, without the need for moving parts or additional power.
Examples: Heat sinks, thermal pads, heat spreaders, and metal chassis are common passive cooling components. These components conduct heat away from hot spots and radiate it into the surrounding environment, allowing the device to cool down passively.
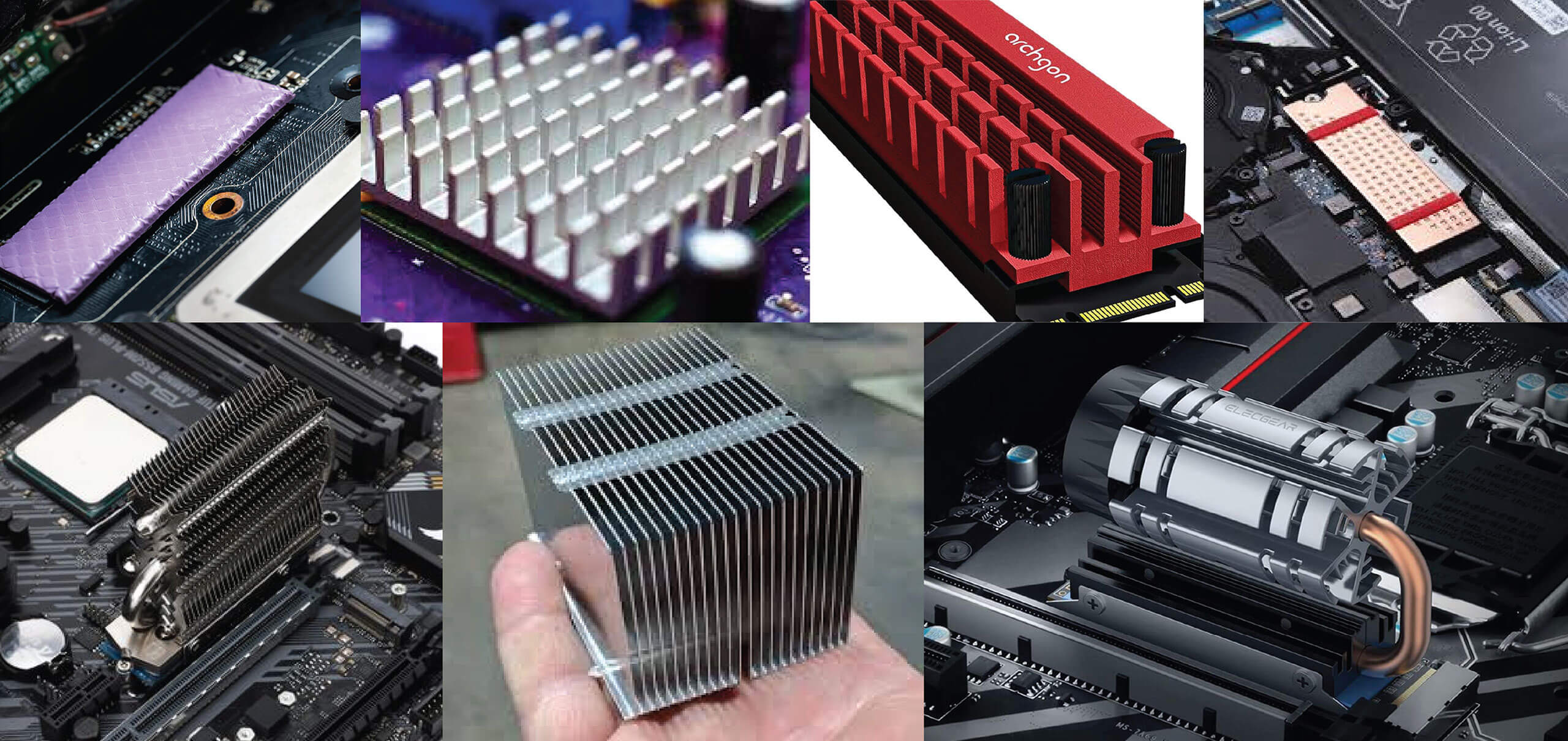
Limitations:
- Limited Performance: The limited ability to remove heat means that performance is throttled to prevent heat related damage to the device and high skin temperatures.
- Limited Cooling Capacity: Passive cooling may not be sufficient for dissipating large amounts of heat generated by high-performance devices.
- Large Heavy Devices: Devices needing higher-performance require large form factors and heavy heat sinks to dissipate heat.
Advantages:
- Limited dust: with no moving parts such as a fan, dust is not actively pulled into passively cooled systems, however dust does still collect on heat sinks reducing their heat dissipation efficiency.
Active Cooling:
Principle: Active cooling involves the use of mechanical moving parts, such as fans or pumps, to actively move air or liquid coolant across heat-generating components, enhancing heat dissipation.
Examples: Fans, blowers and liquid cooling systems (e.g., water or refrigerant-based are common active cooling solutions.
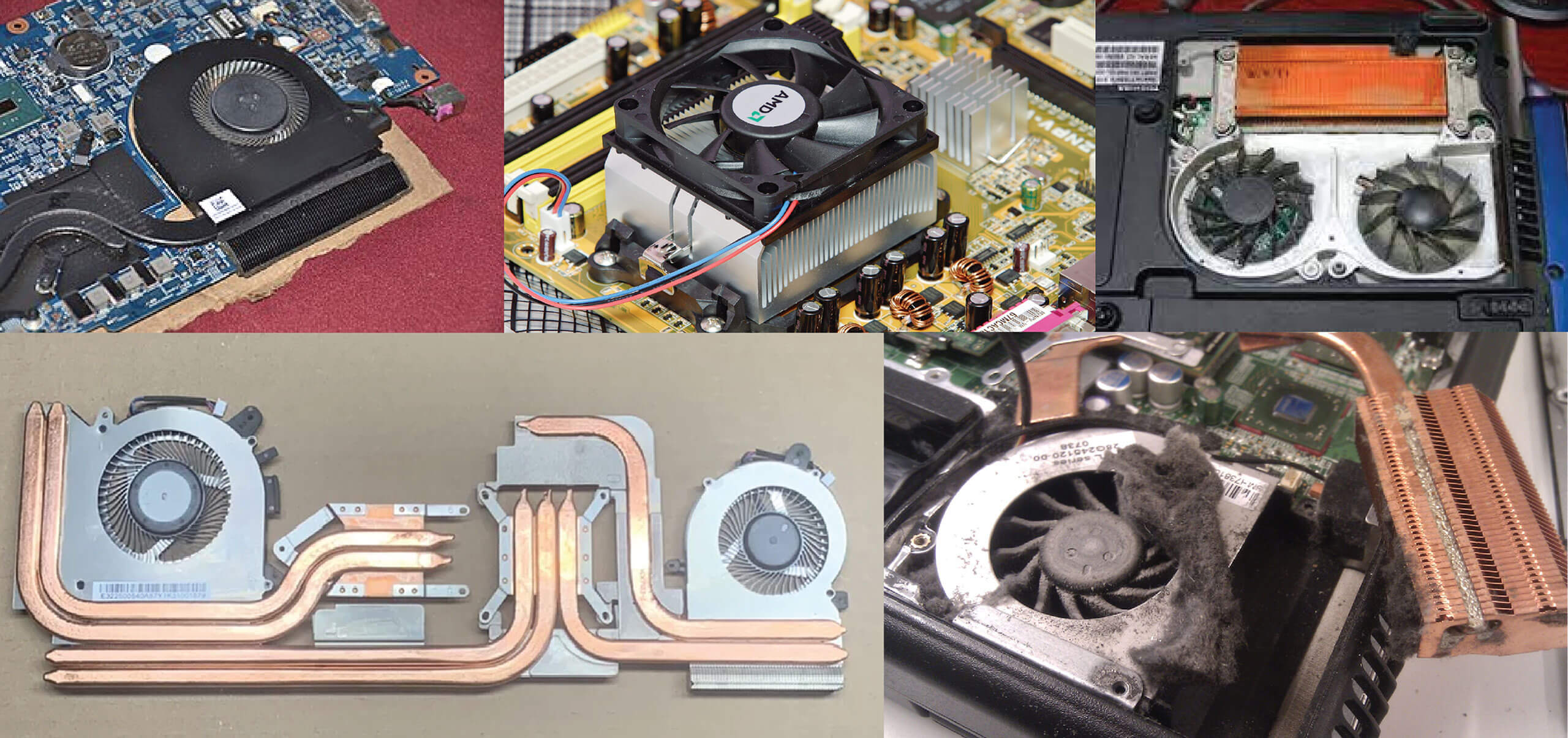
Limitations:
- Reliability Concerns: Active cooling systems with moving parts may be prone to mechanical failures due to wear and tear over time.
- Noise: Mechanical moving parts such as fans can generate undesirable noise during operation.
- Size: Removing large amounts of heat requires larger sized fans, which increase the electronic device size.
- Weight: Heat sinks and fin stacks, critical components of traditional active cooling systems, add additional weight to the device.
- Dust Concerns: Fan based active cooling systems require open inlet vents that result in dust being dragged into the device wreaking havoc.
- Vibration: Mechanical devices with moving parts such as fans generate vibration that can impair device performance.
Advantages:
- Performance: If noise, size, weight, dust and vibration concerns are discounted, active cooling can help the electronic device reach good performance levels.
Solid-State Active Cooling:
Principle: Actively moving air to remove heat without mechanical components, the first product in this category, AirJet uses a piezoelectric MEMs design to achieve active heat dissipation.
Examples: AirJet.
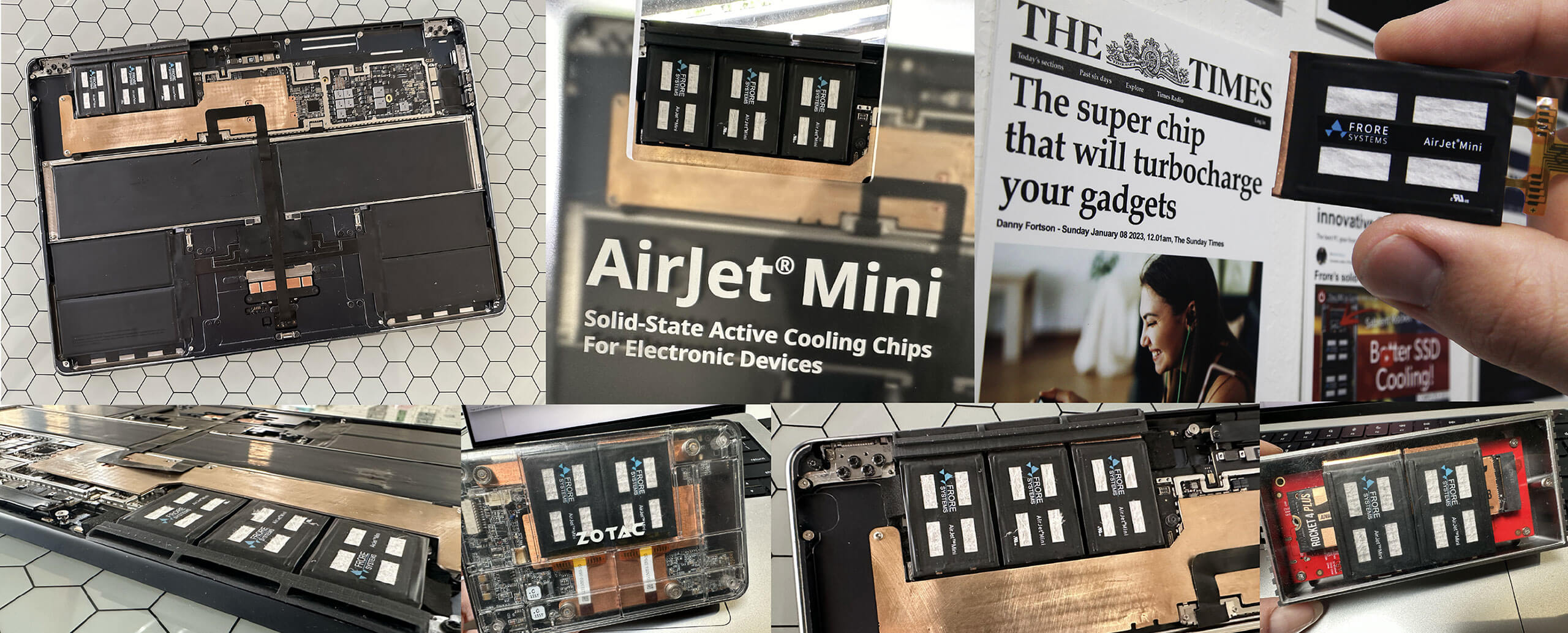
Limitations:
- None: Compared to traditional passive and active cooling, solid-state cooling incurs none of the limitations of either passive or active cooling.
Advantages: Solid-state active cooling addresses the traditional limitations of both active and passive cooling approaches as outlined below:
- Increased Cooling Capacity: AirJet chips can be added in an array, multiplying their heat removal capacity for higher performance applications.
- Higher efficiency: AirJet chips feature jet impingement, vertical jets of air that destroy the boundary layer, enabling more efficient transfer of heat.
- Zero Noise: With no mechanical components Airjet is silent.
- Reduced Reliability Concerns: AirJets lack of mechanical components, eliminates concerns about mechanical failures or wear and tear over time.
- Zero Dust: The incredibly high backpressure of AirJet supports air flow and active heat removal in dustproof devices where the air inlet vents are covered by dust guards.
- Vibration Free: As a solid-state solution with no moving mechanical parts, solid-state cooling is completely vibration free.
AirJet Solid-State Active Cooling has introduced a new era of heat removal, overcoming many of the thermal limitations manufacturers and consumers have lived with for decades. Consumers finally have a choice that can meet all their needs and realize the full performance they pay for.'
It’s time for a revolution against size, thickness, noise, weight, vibration, and dust…. Contact us to find out more.